Process
Process monitoring
for joining processes
Regardless of the industry, it is important to ensure precision and accuracy in the joining process. Failure to do so can have serious consequences, including damage to the company’s image, reduced quality, and even personal injury.
Even seemingly „small“ negative effects of a lack of process control have significant consequences in the grand scheme of things. To ensure that high scrap rates and time-consuming inspection procedures are a thing of the past, it is advisable to invest in process monitoring and optimization.
The focus here is on short, fast joining processes where maximum precision is required.
The aim of these
process optimization measures is to
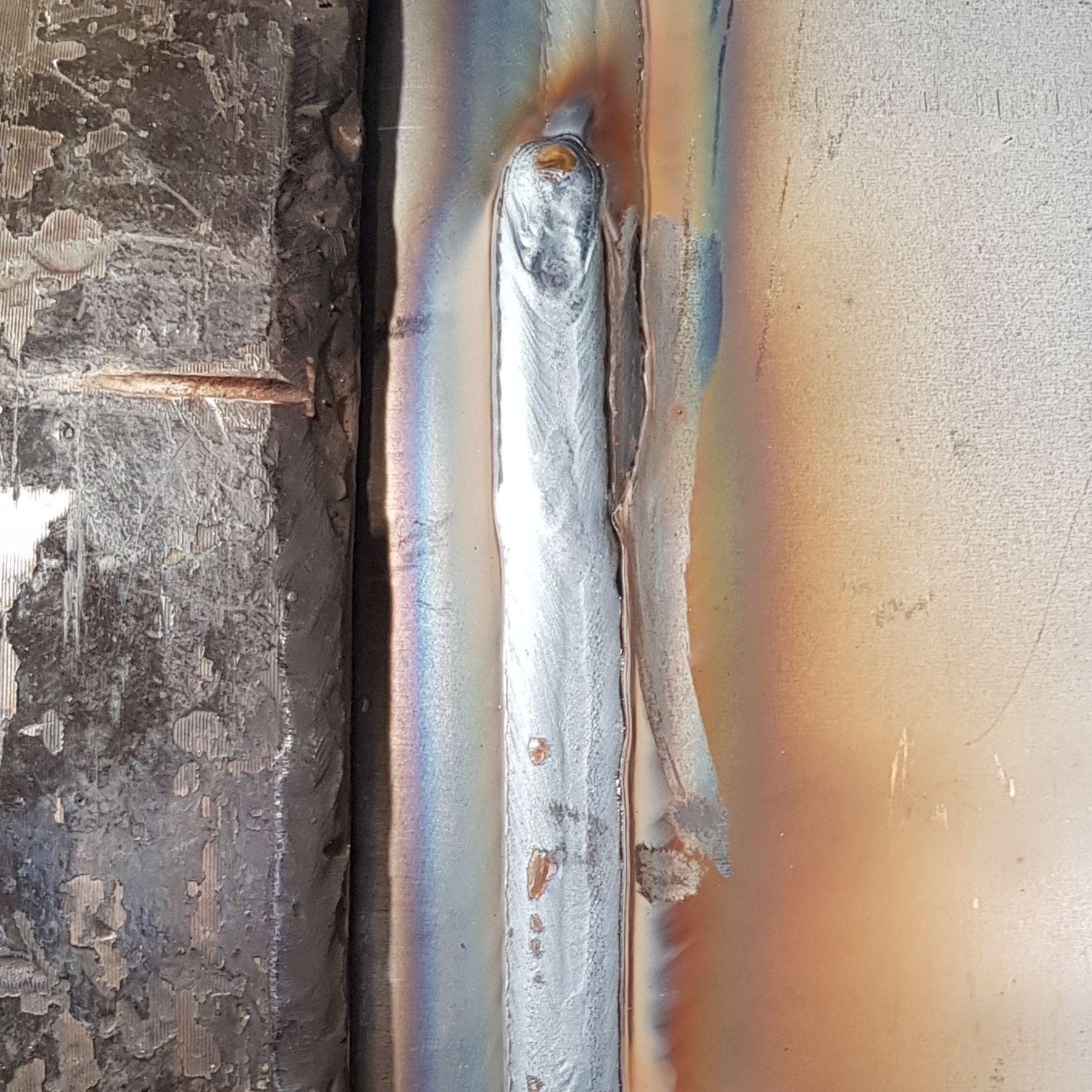
Detect welding defects during the joining process without loss of cycle time
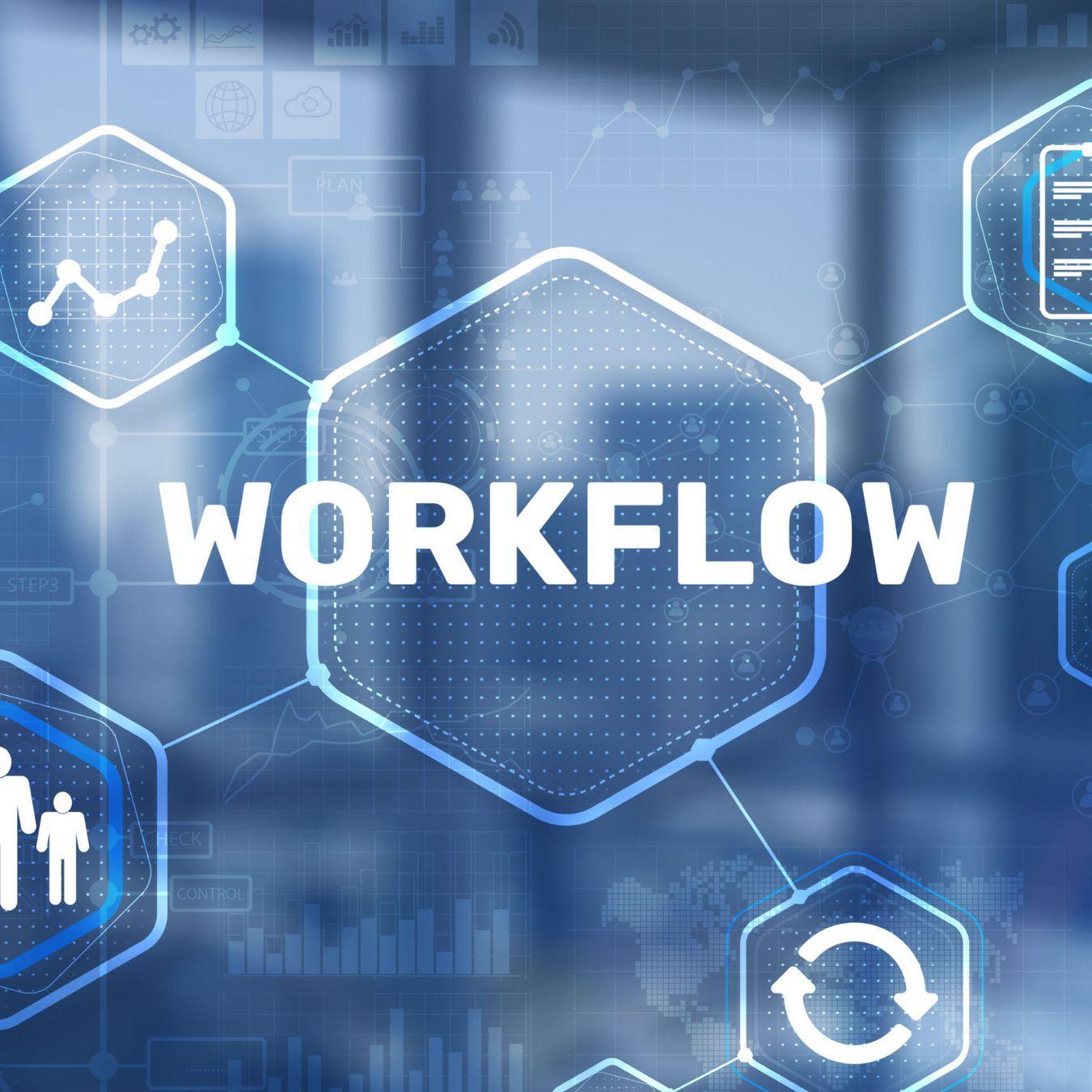
Enable 100% traceability
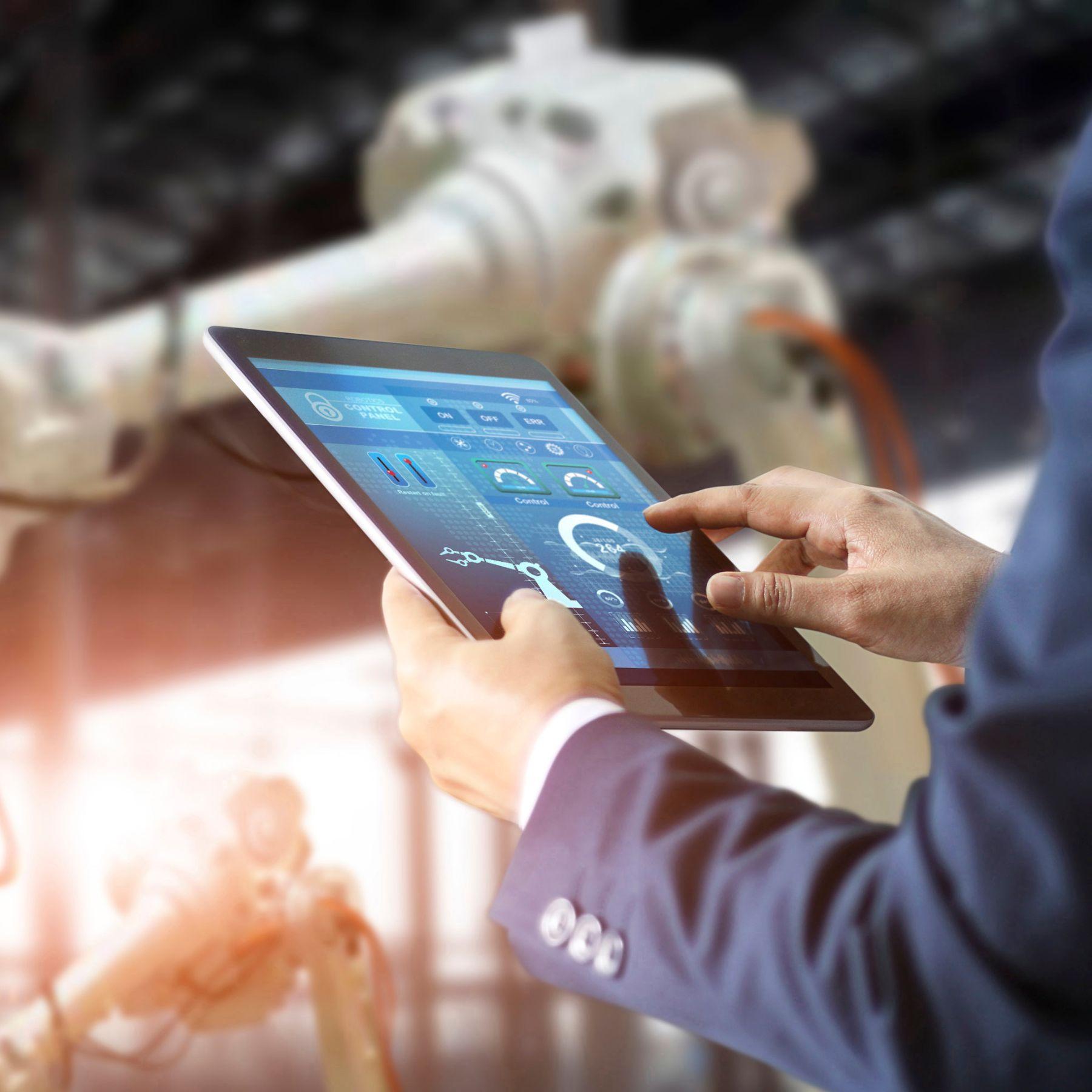
Reliable and repeatable process monitoring
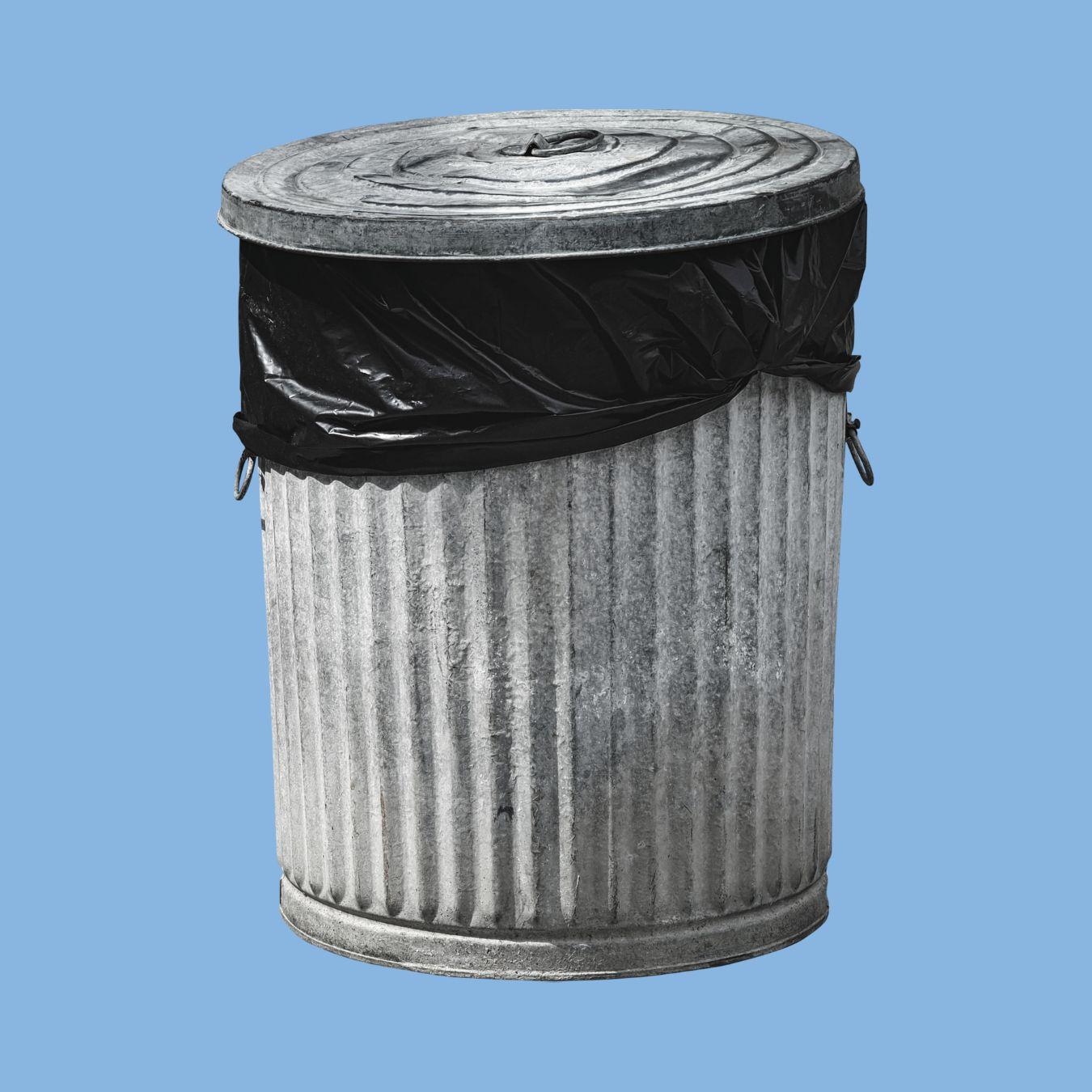
Reduce and eliminate scrap to the greatest extent possible
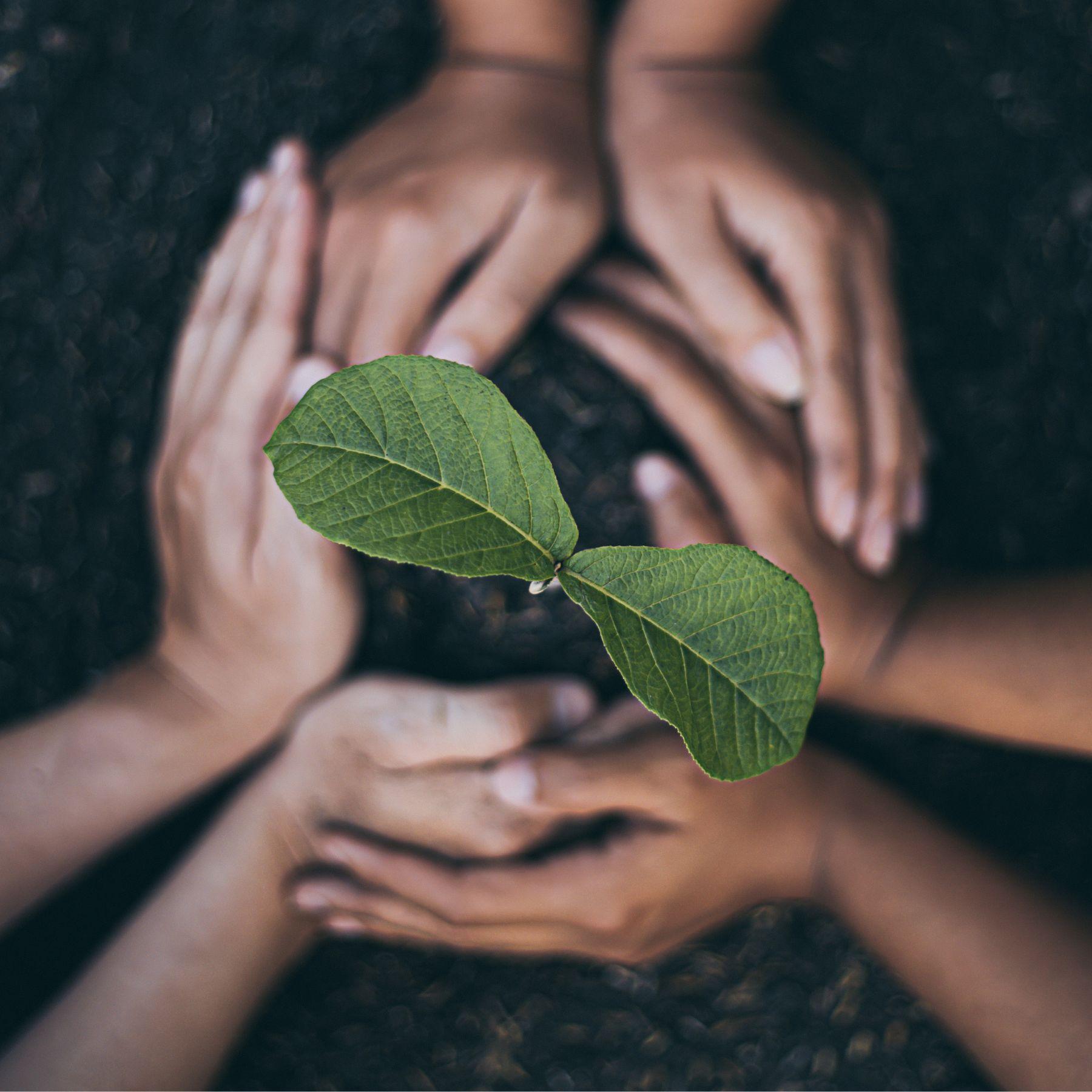
Use resources wisely and save
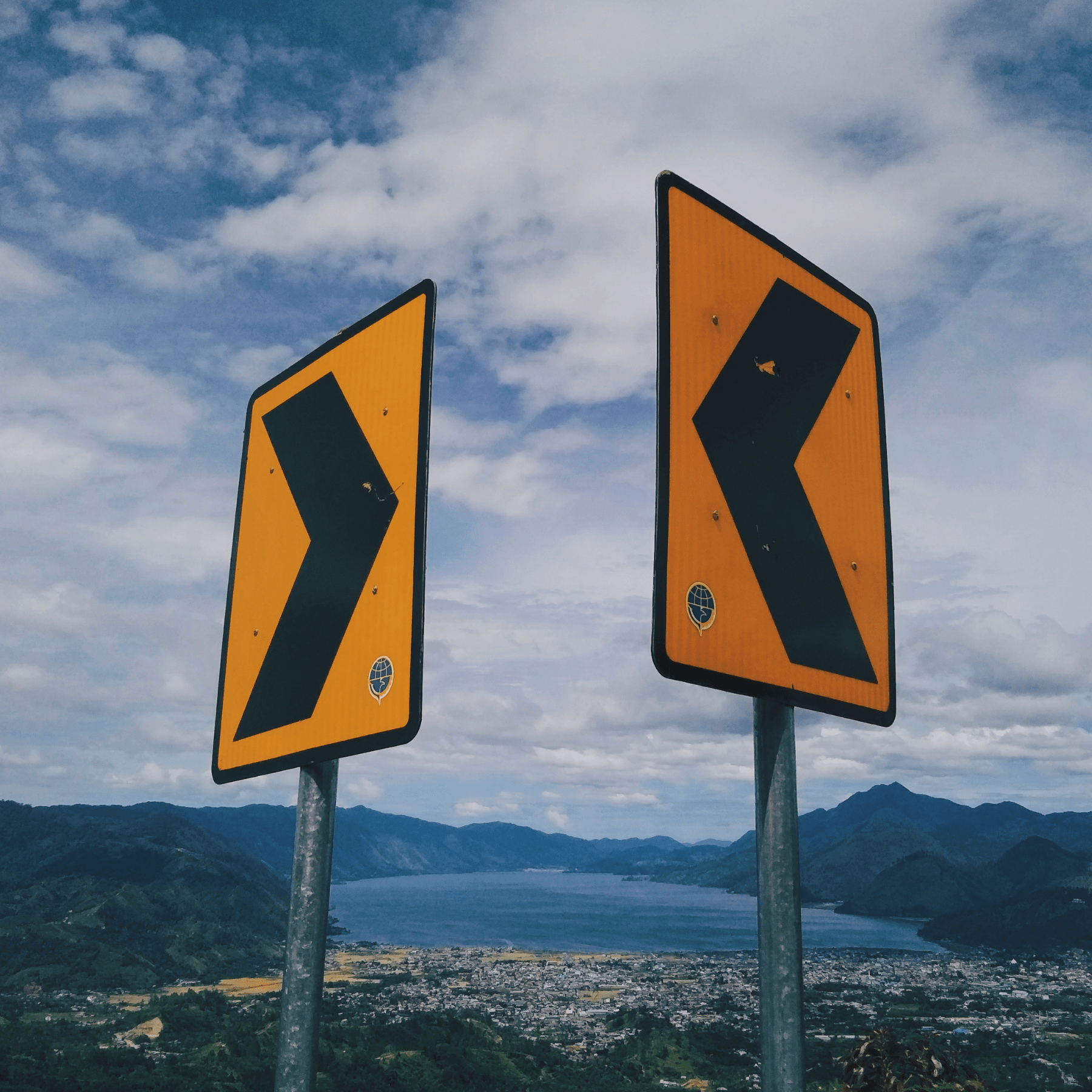
For early detection of process drift
Process optimization in several steps
.01
Process definition
The first step to process improvement is to identify the process that needs improvement.
Which process is currently causing the most defects?
Where can the weld quality be improved? Where should additional resources (human and material) be saved in the future?
Once this process has been defined, it can be worked on.
.03
Develop optimization strategies
The development of optimization strategies is based on the results of process analysis and aims to eliminate identified problems and improve process efficiency.
It involves selecting appropriate methods and tools, planning changes to process flows, and setting performance goals.
This phase also considers the potential impact on the overall system and the resources required to implement the strategy.
The resulting strategy provides a structured and focused plan for implementing process improvements.
.02
Process documentation & analysis
Process documentation is the step where the current work process is recorded in detail.
It includes the recording of all specific steps, roles involved, tools used, and expected results. This documentation provides a clear and complete view of the process, which serves as the basis for comprehensive analysis and subsequent improvement actions.
Processes need not, and in most cases cannot, be documented manually. Instead, sensors such as the WLDR sensor can be used to map the process and display it as a diagram. Photos, X-rays and documented observations are also suitable.
.Fazit
PROMOS
In order to avoid having to document the individual steps of process optimization manually with paper and pen, process optimization software such as PROMOS is a good choice.
Not only does it provide a good overview of the individual processes, it also makes the results comparable and displays all the data at once in a clear dashboard.
Effects of
Process monitoring
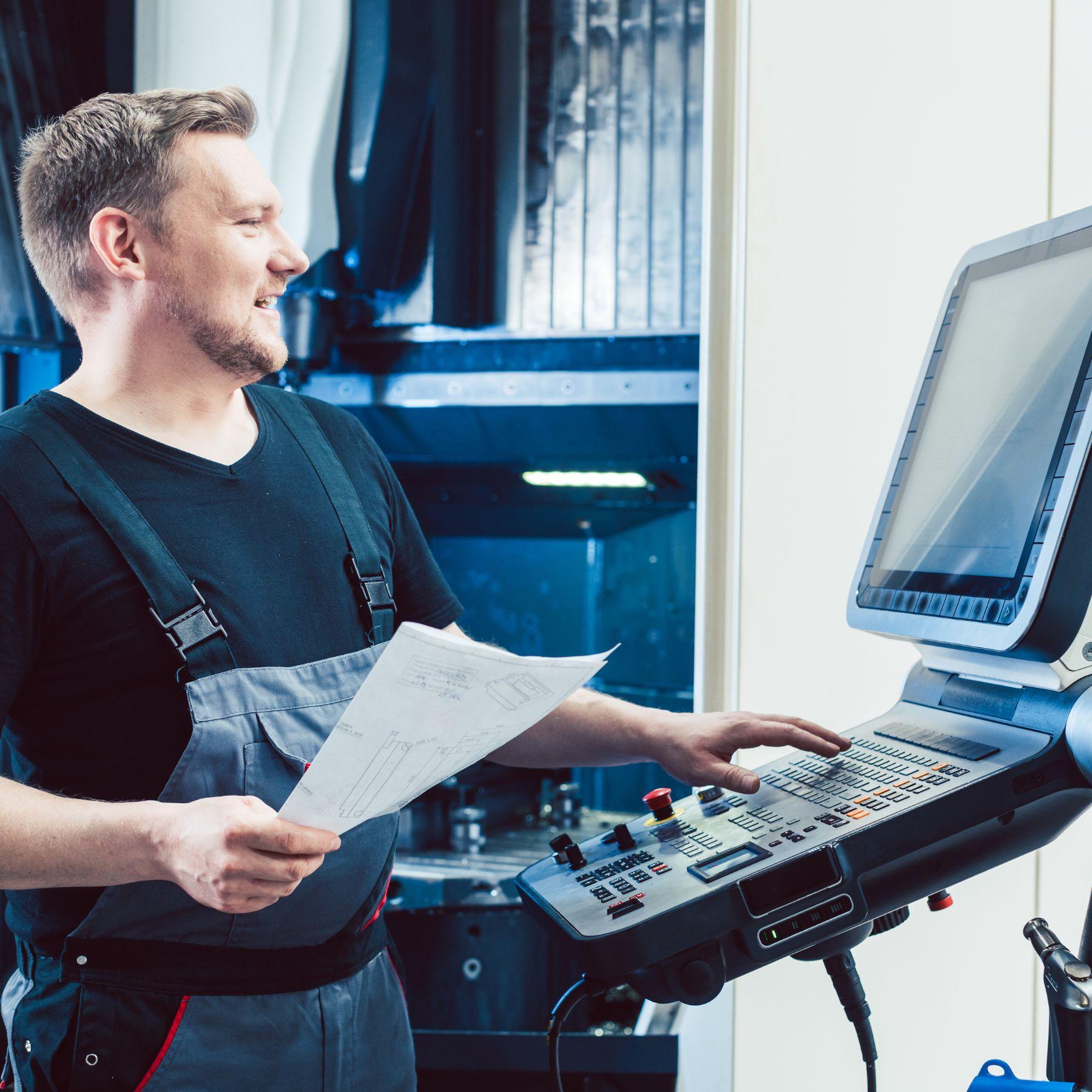
Well-trained specialists take on higher-value tasks rather than „assembly line“ work.
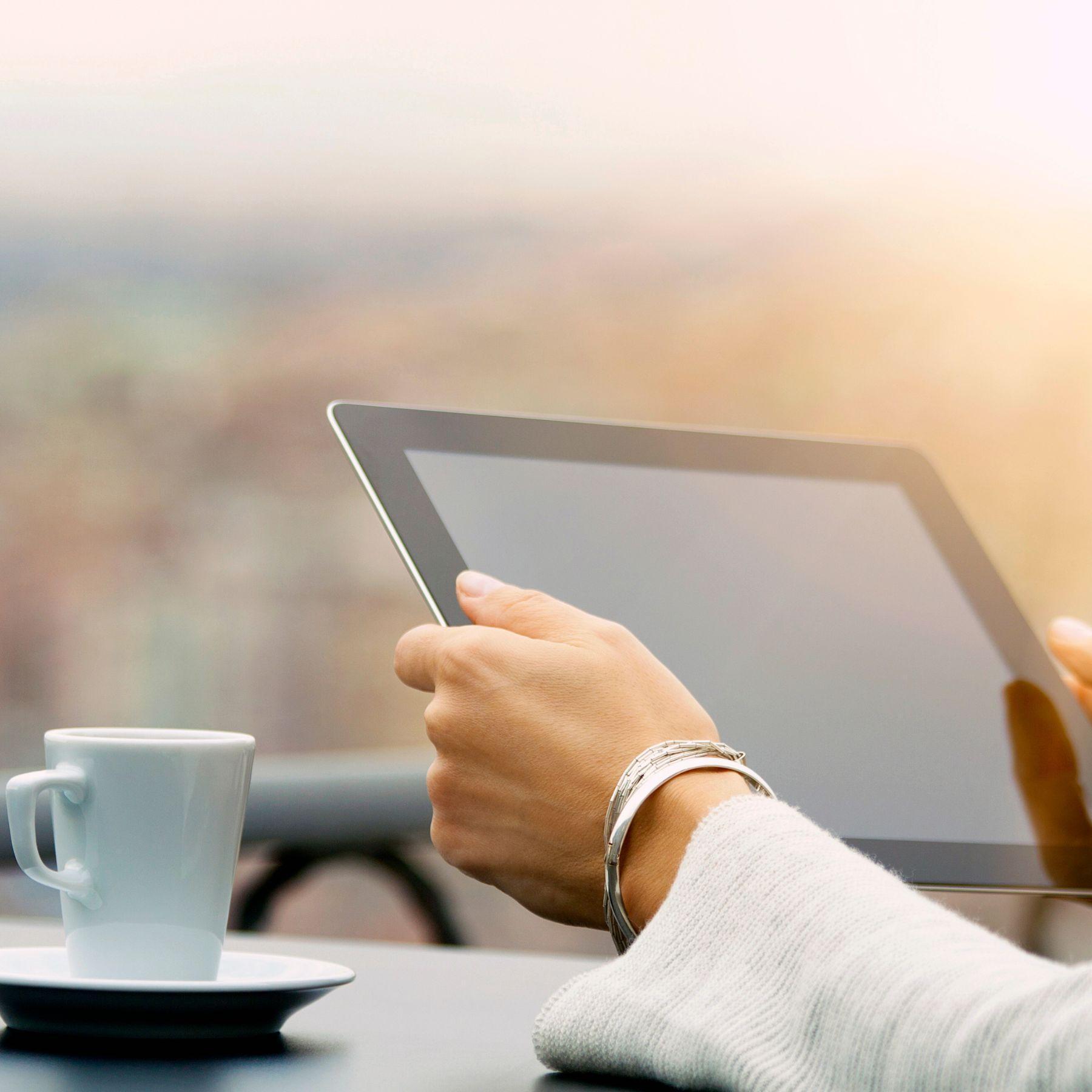
Ease of use allows for more flexible time and location assignments.
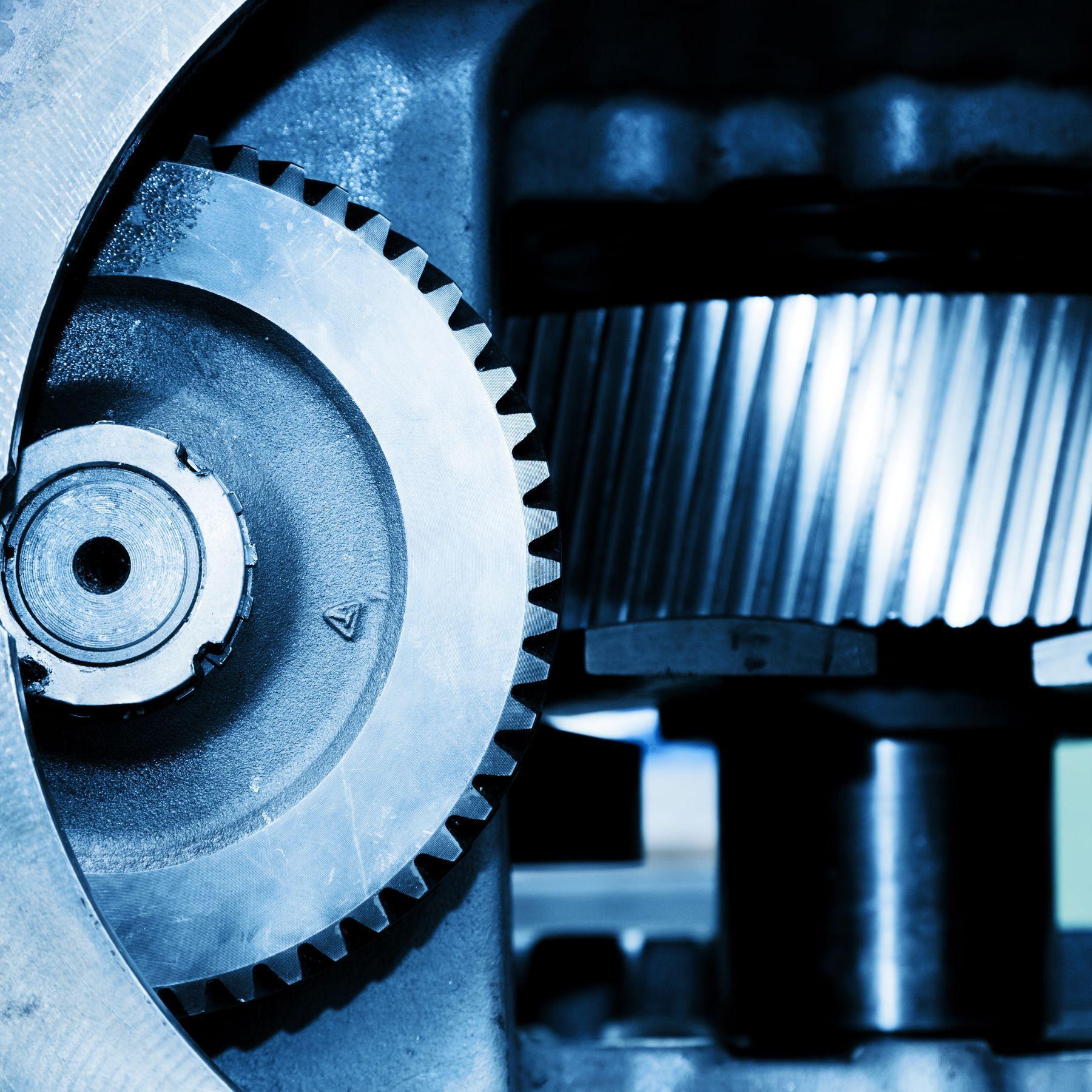
With the burden of monitoring off your shoulders, you can focus on optimizing your processes.
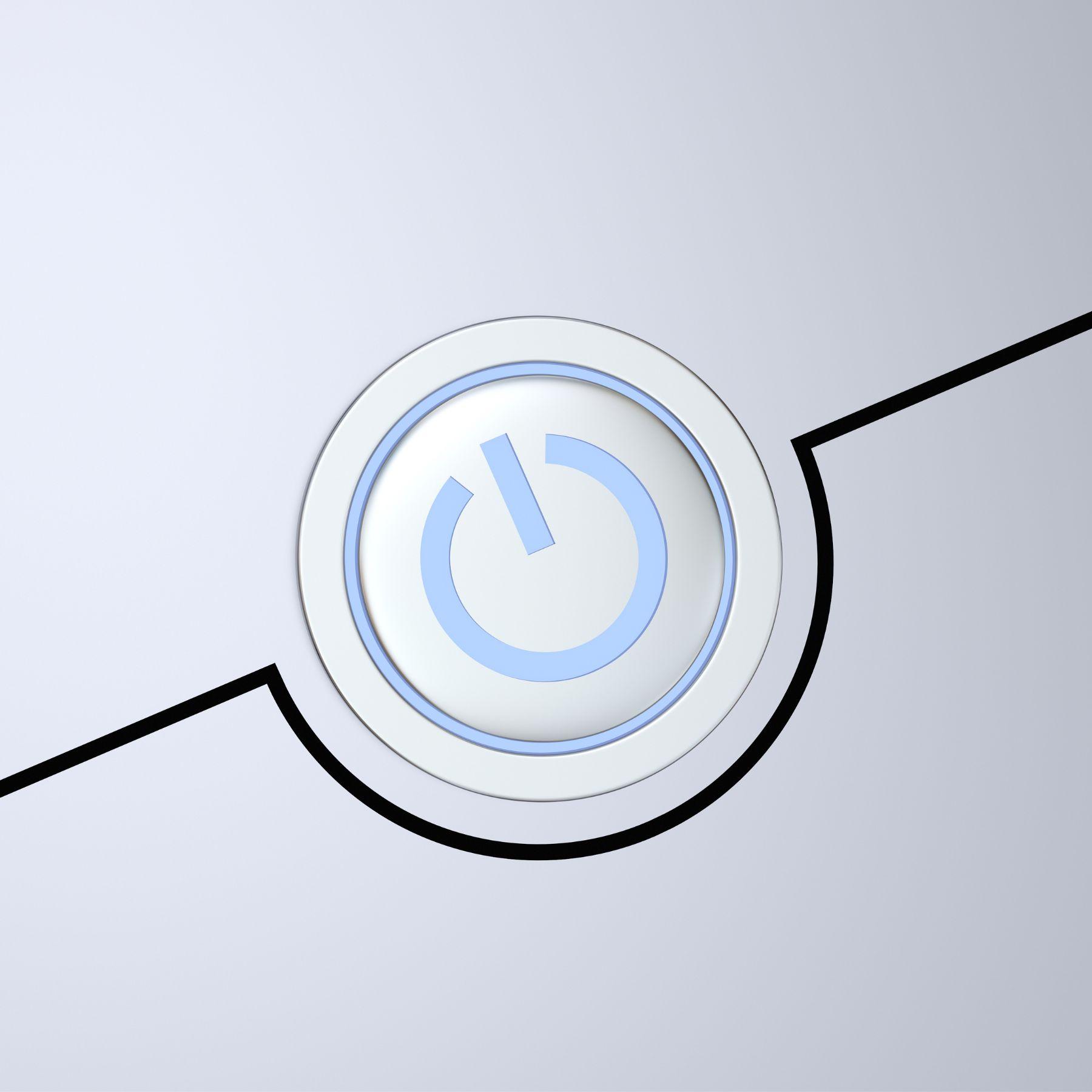
A plug-and-play solution allows process monitoring without rebuilding the entire production line.
weldmetrix GmbH
elevating standards, monitoring success
Headquarter
Gutheil Schoder Gasse 17
Techpark Vienna
1230 Vienna
Austria
Copyright © 2023 – weldmetrix GmbH